Bedford Manufacturing Facility Vital to Data Storage Industry: Q&A with Kim Ryder, VP of Finance & Operations
In this executive Q & A, Kim Ryder, VP of Finance & Operations, discusses her role at FUJIFILM Recording Media U.S.A. and how Fujifilm’s Bedford Manufacturing facility plays a vital role in the world of data storage now and in the future.
Q: Explain your role as VP of Finance and Operations
First, I’d like to start by wishing our readers a healthy and happy Holiday season!
My primary role is to drive and maintain operational excellence within the Bedford Manufacturing facility to deliver products and solutions that provide exceptional customer satisfaction. It’s not a trivial task! Many of the world’s largest technology companies depend on us to deliver premium quality, high-density tape cartridges that back up the internet and safely and cost-effectively retain user content for decades.
Q: What are some of the sustainability initiatives you have undertaken at Fujifilm?
The FUJIFILM Groups’ approach to creating a Sustainable Society is to resolve social issues through our business activities and consider society and the environment in our business processes. In response to the corporation’s vision, in November 2013, we installed a 1,870 solar panel array on the roof of our Bedford Manufacturing Facility. Our solar installation has produced 4,858,000 kWh since its inception. That’s the equivalent amount of energy used by 9,700 homes during an entire month. It’s also the equivalent of a reduction of 2,915 metric tons of carbon dioxide per year. Over 20 years, this would equal the carbon sequestered by 11,870 acres of U.S. forest in one year.
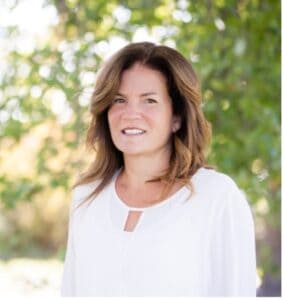
“With over 3,000 bulbs replaced, we estimate a savings of 400,000 kWh this year!” – Kim Ryder
In addition to our solar panels, we converted to LED lighting in our manufacturing facility. By converting to LED bulbs, we will reduce our carbon footprint by approximately one-third, minimize daily maintenance work, decrease our UV emissions to zero, and be more energy-efficient overall. With over 3,000 bulbs replaced, we estimate a savings of 400,000 kWh this year!
Of course, tape is the greenest form of data storage available, consuming 87% less energy than the equivalent amount of hard disk drive storage. When you look at the total lifecycle from raw materials to production to distribution, to usage and disposal, the reduction of CO2 goes up to 95%.
Q: What role does the Bedford Manufacturing facility play in the IT industry?
Actually, Bedford is the world’s largest manufacturing facility of Linear Tape-Open (LTO) high-capacity data cartridges. Our products provide the world’s leading companies with high-capacity data storage solutions to help them manage the digital transformation’s exponential data growth. As a result, organizations and enterprises of every shape and size rely on our products for reliable, long-term, eco-friendly and cost-effective data protection and retention. With data as the new currency and lifeblood of the digital economy, Fujifilm plays a unique role in serving the dynamic IT industry with innovative data storage solutions.
Q: What are some of the challenges you face?
We face a lot of similar challenges as other manufacturing facilities. The disruption in the domestic and global supply chain has forced us to rethink our overall supply chain strategy. We’ve had to tighten our inventory controls, strengthen our communication with our suppliers, look for and qualify alternative vendors, and heavily rely on our employees for innovative solutions to overcome the day-to-day challenges. However, our agile response to the disruption has allowed us to maintain exceptional customer service to our customers.
Our second most significant challenge is the labor market. We’ve all heard the terms the “great resignation”, or the “great reshuffle”, or the “great renegotiation”. We often wonder, “where have all the employees gone”? However, with employees being our biggest asset, we’ve had to focus on not only recruiting but retaining our staff. We’ve had to take a hard look at our organization and recognize the need for and put together a succession plan that includes accelerated training and development for immediate changes to some of our business functions. We’ve also made several changes in our work-from-home policies, implemented flexible work schedules, and offered additional benefits. In our manufacturing area, we’ve increased incentives and created new positions allowing for growth and development. We’ve come up with innovative ways to continue to engage our employees in activities while staying safe. We are focused on providing a positive recruiting and onboarding experience for our new employees.
Q: What are the key advantages of today’s modern data tape technology?
There are many advantages of today’s modern tape technology. But I think the big ones have to do with cost savings, capacity, sustainability, and cyber security. Tape has the lowest cost per terabyte of data stored or the lowest Total Cost of Ownership (TCO). Tape’s high capacity per cartridge and low energy consumption contributes to its low TCO. The low energy consumption profile of tape makes it eco-friendly. Today, energy-intensive storage solutions like hard disk drive technology are giving way to eco-friendly tape solutions that consume less energy and produce less CO2 emissions. This helps the IT industry to reduce its impact on global warming and climate change. Finally, in response to rapidly increasing cybercrime incidents like ransomware, high-capacity tape offers an efficient and cost-effective way to prevent unauthorized access by securing data in offline, offsite locations. This is a practice that is now recommended by the FBI and other Federal agencies like CISA.
Q: What makes Fujifilm Bedford an attractive place to work?
For starters, we have a bright future! As the IT industry has entered the age of massive zettabyte storage, Fujifilm and IBM together have demonstrated future technology enhancements for increasing the capacity of tape systems beyond 500 TB per cartridge, securing a bright future for tape for decades to come in long term data protection and retention.
Secondly, our work environment is like no other – it’s based around respect, trust, and diversity with a comfortable and positive atmosphere. We keep the work challenging and rewarding, with opportunities to learn and grow. Our consensus-driven management style and strong core values set us apart from most other companies. Fujifilm strives to offer a healthy work environment that promotes individual responsibility and growth, a collaborative spirit, and an atmosphere that encourages learning, professional development, and achievement.
Finally, with data as the new currency and lifeblood of the world’s leading companies, Fujifilm is uniquely positioned to serve the dynamic IT industry with innovative solutions for a long time to come.
For more information, visit: https://datastorage-na.fujifilm.com/lto-tape-data-storage/